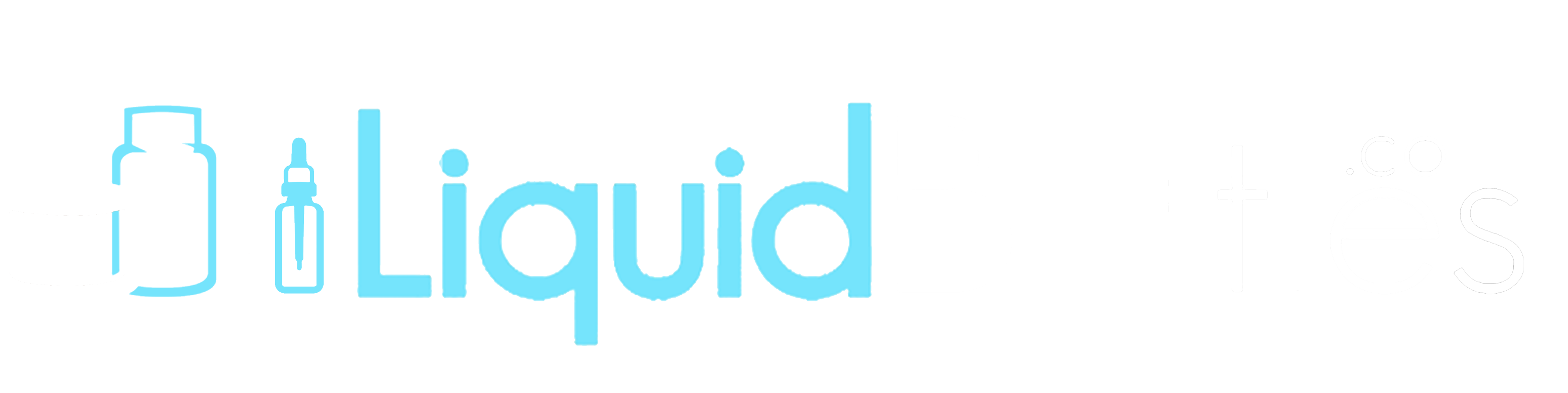
- 2021 51st Avenue East
Suite 100
Palmetto, FL 34221 - 888-222-5232
- Info@LiquidBottles.com
- Mon-Fri: 9:00-6:00 (EST)
Posted Tuesday May 3, 2022
Have you wondered what people mean when they talk about shipping delays due to the supply chain?
On average, it currently takes 115+ days from when a Chinese manufacturer says products are ready to be put on a container to when the products are actually delivered to a US port. However, it only takes 15-20 days for the ship to cross the Pacific. The rest of that time is for the products awaiting containers and clearance in China and awaiting portage/clearance in the US and offload onto trucks and the truck delivery. This is over twice as long as it was to receive goods three years ago. Also, costs to get a container from China delivered to the US are now up to 7 times what they were only three years ago. So, why is it taking so long for products to arrive and why is it now exponentially more expensive?
There are many reasons for the delays and price increases. One of the main reasons is the sheer volume of goods going in and out of the US terminals. Increased traffic on a shipping infrastructure that has not been updated/expanded to accommodate the growing demand is causing a pinch for everyone involved in the shipping process from manufacturers to carriers to distributors and ultimately to end consumers.
And, let us not forget the global pandemic that started in late 2019 and still plagues us today, with ripple effects of manufacturing shutdowns, port and facility shutdowns, and worker shortages all contributing to the waves of supply/demand imbalances of container shortfalls, bubbles of congestion, and increased costs.
To highlight these challenges further, an example of one part of the chain that is breaking down is the congestion and outdated infrastructure is causing nearly 50% of appointments to pick up containers at the truck yards to be missed. Containers arrive into the port terminals and are then typically brought to truck yards where to be loaded/picked up and delivered to the end consumer. Higher volumes into these yards are bumping against space regulations limiting how creative the yards can be on stacking the containers to maximize space and efficiency. This causes an issue with available space and some containers then must be left on the chassis. The effect from this is a chassis shortage, so truckers cannot get a chassis to deliver the consumer. Additionally, truck yards operate with limited one-hour windows for pickup, and the chassis shortages, driver shortages, and just pure traffic jams in the yards make this part of the supply cycle extremely challenging and understandably backlogged.
Not only are there delays in getting the products to the distributors to sell, but getting the products into the hands of the consumers is also facing dramatically reduced capacity and effectiveness. Domestic shipping carriers attempt to meet the demands of the increased volumes, but with terminal congestion, employee shortages, chassis shortages, and driver shortages, complicated by slow and inconsistent information on shipment status, it is nearly impossible for shipments to be tracked with accuracy or delivered in previously reasonable timelines.
Additional delays are possible and even expected in the upcoming months. The labor union contract with the west coast ports from Mexico to Alaska are set to expire July 1st of this year. Routine negotiations are underway with intent of working out a new contract before then. However, if the parties are unable to reach agreement, the west coast ports would close. This happened before for a few months back in 2015. This would mean all ships needing to go through the Panama Canal, causing congestion there and congestion to ports to the east such as TX, FL and other gulf coast locations, further compounding already stretched resources in those areas.
Also, starting January 1st 2023, all cargo ships across the world will be required reduce their carbon emissions by 13% per the UN’s International Maritime Organization (IMO). Currently, the only way this can be achieved is if the ships reduce speed by 30%. This would then increase the delivery time of containers making it to port by 30%. This might only add 5 days to the 15-20 days for delivering to west coast ports. But for other ports like FL, this could add anywhere from 10-20 days, depending on the port.
We understand and share the frustrations and challenges of trying to get what you need when you need it and request that we all be patient as we ride the storm of these changes together. We will do our best to keep our customers updated as we continue to watch as these dynamics unfold.